How To Manufacture a Carbon Fiber Stick
How To Manufacture a Carbon Fiber Stick
When a hockey player winds up to take a slapshot top corner, they want to make sure that the stick in their hands is of the best quality, both in how durable it is, and how it improves their shot. Not only do you want the shot to go exactly where you are aiming, but you don’t want your stick to break on you as you’re taking the shot either.
For over a century, hockey sticks were made with wood as the main material. It offered enough strength and durability, while also being a little flexible so that the stick whips forward on the shot and adds velocity on the follow-through. But over the last 20 years, wood has been replaced by composite carbon and graphite materials that give the sticks more flexibility, while being a fraction of the weight, and having almost as much durability as wood.
The stick nowadays are made with carbon fiber which is a fabric-like material almost like cloth. It is made up of thousands of carbon threads combined with a plastic resin that gives the material strength and flexibility. The sticks are usually made in two different pieces, the shaft, which is the long part that is held, and the blade, which is the curved bottom part that touches the ice and puck. At one point in the manufacturing process, the pieces will be fused together to create one continuous piece, and because of this, carbon fiber hockey sticks are often called “one-piece” hockey sticks.
While there are many steps to creating these new carbon hockey sticks, the whole process only takes about two hours from the first sheet of carbon fiber, to the logos and final layer of paint.
To create the sticks, manufacturers will take sheets of the carbon fiber material and overlap them with other sheets going the opposite way to create an intersecting pattern that links the fibers and creates a sturdier material. These sheets will then be pressed through hot rollers to melt the plastic resins in them and form a bond between them. With these doubled-up sheets, a person will cut them into pieces and roll sheet after sheet together (usually about 20 sheets) around a shaft-shaped mould. The person has to be sure each sheet is pressed firmly and there are no bubbles in the shaft, or it will cause the stick to break much easier.
While the shafts are being made, the blades are created as well. They start with a foam-like core that allows the blade to take impact from passes and shots, while still being light and having some give to it. You want the puck to be able to spring off the blade and create more velocity, while also being lightweight. The foam core will have a curve to it, either to the left or to the right, and this will result in the curved shape that you see in the finished product. Different curves allow for different types of shots, stick handling, and passing types. A hard shooting defenceman will want a different curve than a sniper winger, but it all comes down to individual player preference. Around the foam core, more sheets of pressed carbon fiber are wrapped around, usually as many as 35 per blade.
Once enough sheets are rolled over the shaft and blade, the blade is slid to fit into the hollow shaft, and they are placed into a metal mould to be baked in an oven. Air is also blown into the stick to help it keep its shape and not get flattened. The temperature is very important and the sticks are baked in compression chamber that is heated to about 300 degrees Fahrenheit for about 30 minutes to an hour. The shafts will cook and compress in there to form one strong, “unbreakable” bond of carbon fiber, and then are taken out and cooled. These sticks are then tested by machines to check their flex and make sure they do not break. Sticks are created with different flexes for different types of players. A bigger, stronger player will use a stiffer flex, while a smaller, weaker player will use a stick that flexes more.
The sticks that come out are a little rough, so they have to have edges sanded down a bit, and then the stick is polished and primed for painting. The sticks are painted by hand depending on the brand and model. This usually takes many layers of paint and different colours. Once painted, logo stickers will go on the side of the shaft with the brand logo, model, and information such as the flex, blade type, and serial number. Finally, the stick will then be finished with a protective coating that gives the stick one extra layer of protection. If the stick is meant to have a grip layer on the outside, it will be applied now as well.
Once the sticks are finished, they will be shipped off to stores and players for their on-ice sniping pleasure. Many companies now even have custom stick options where you can select your flex, curve, length, paint job, and more. They are more expensive this way, but to get a stick that fits your perfect specifications, it can definitely be worth it.
Latest News
Contact Us
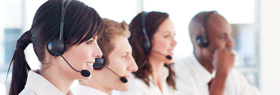
Name: Michael
E-mail: [email protected]
Skype: michael.zhang89